Comprehensive Welding Inspection Service for High-Performance Welding
Comprehensive Welding Inspection Service for High-Performance Welding
Blog Article
Unlocking the Secret Kinds Of Welding Services for Your Projects
In today's landscape of varied welding solutions, understanding the subtleties and applications of various welding techniques is vital for successful job execution - Welding Inspection Service. By unwinding the essential types of welding services available, one can navigate the ins and outs of choosing the most appropriate approach to make sure precision, efficiency, and quality in welding projects.
Typical Welding Techniques
Numerous generally used welding techniques play important duties in various industrial markets. Among one of the most commonly utilized methods is Gas Steel Arc Welding (GMAW), additionally called MIG welding. This method includes feeding a cable electrode through a welding weapon, which is connected to a power source and shielded by a gas mixture to secure the weld pool from climatic pollutants. GMAW is valued for its adaptability, high welding speeds, and capability to bond different metals.
An additional popular welding strategy is Gas Tungsten Arc Welding (GTAW), frequently referred to as TIG welding. TIG welding utilizes a non-consumable tungsten electrode to develop the weld and needs a separate filler product. This technique is preferred for its ability, control, and accuracy to generate high-grade welds on slim materials.
Secured Metal Arc Welding (SMAW), or stick welding, is an additional important method where a flux-coated electrode is used to create the weld. SMAW is known for its simpleness, convenience, and suitability for on-site and outside welding applications. These common welding methods are vital for making structures, equipment, and different tools across industries.
Advanced Welding Procedures
Advanced welding processes incorporate advanced techniques that push the limits of traditional welding methods in terms of versatility, efficiency, and accuracy. One such process is laser beam welding, which utilizes a concentrated beam to sign up with metals with minimal heat-affected areas, making it perfect for high-precision or fragile tasks. In addition, electron beam welding employs a high-velocity electron beam of light to develop deep welds in thick materials, supplying remarkable toughness and high quality.
Furthermore, friction stir welding is a solid-state joining process that utilizes a revolving tool to produce frictional warmth, bonding materials without thawing them. This approach is particularly valuable for joining light-weight alloys with remarkable mechanical properties. An additional cutting-edge technique is ultrasonic welding, where high-frequency ultrasonic resonances are utilized to produce solid-state welds in plastics, steels, and other materials, offering fast and clean signing up with solutions.
These advanced welding procedures satisfy a diverse series of industrial demands, supplying effective, premium, and specific remedies for numerous tasks, from aerospace elements to automotive parts and past.
Specialized Welding Applications

Automated Welding Solutions
In modern industrial setups, the application of automated welding remedies has revolutionized production procedures by improving efficiency and precision. Automated welding systems utilize advanced technologies such as robotics, computer system numerical control (CNC), and expert system to perform welding jobs with very little human intervention (Welding Inspection Service). These systems supply many benefits, consisting of boosted performance, boosted weld high quality, and minimized production costs
One trick advantage of automated welding solutions is their capacity to regularly produce high-quality welds, causing improved total product top quality. Additionally, these systems can run continuously, 24/7, without the demand for breaks, resulting in higher result levels and faster task completion times. By making use of automated welding solutions, companies can likewise mitigate the risks connected with human error, making sure higher accuracy and repeatability in the welding procedure.
Moreover, automated welding options are very flexible and versatile to numerous welding applications, from detailed elements to large-scale frameworks. Whether in automobile production, aerospace sectors, or building projects, the combination of automated welding systems provides a competitive edge by improving procedures and delivering premium welding results.
Innovative Welding Technologies
The advancement of automated welding remedies has actually led the way for the integration and development of ingenious welding modern technologies in modern-day commercial applications. One such sophisticated modern technology is laser beam welding, which makes use of a very concentrated beam to join metal parts with accuracy and efficiency. This technique is especially valuable for tasks needing complex welds on products with high melting factors or for applications where marginal heat-affected areas are vital.
One more innovative welding technology acquiring appeal is rubbing stir welding (FSW), a solid-state joining procedure that creates high-strength bonds by creating frictional warm between two items of metal. FSW is commonly used in industries such as aerospace and vehicle for its capability to create welds with exceptional mechanical buildings and enhanced structural integrity.
In addition, electron light beam welding (EBW) is an advanced strategy that find utilizes a light beam of high-velocity electrons to produce exact, deep welds in metal elements. This modern technology is preferred for its capacity to weld different steels and products with differing densities properly. As industries remain to require higher high quality and efficiency in welding procedures, these innovative innovations are poised to play a significant role fit the future of commercial welding applications.

Verdict
Finally, comprehending the crucial types of welding solutions is important for successfully completing a range of jobs. From common welding strategies to advanced procedures, specialized applications, automated options, and ingenious modern technologies, each method provides unique advantages and applications. By acquainting on your own with these different welding alternatives, you can choose one of the most appropriate method for your certain job needs and attain high-quality outcomes.
In today's landscape of varied welding services, comprehending the subtleties and applications of different welding techniques is paramount for effective job execution. By untangling the vital kinds of welding services offered, one can browse the details of selecting the most ideal method to make certain precision, efficiency, and top quality in welding tasks. As we embark on this exploration of welding services, a deeper understanding right into the More hints world of welding waits for, appealing understandings that can boost the end results of your projects.
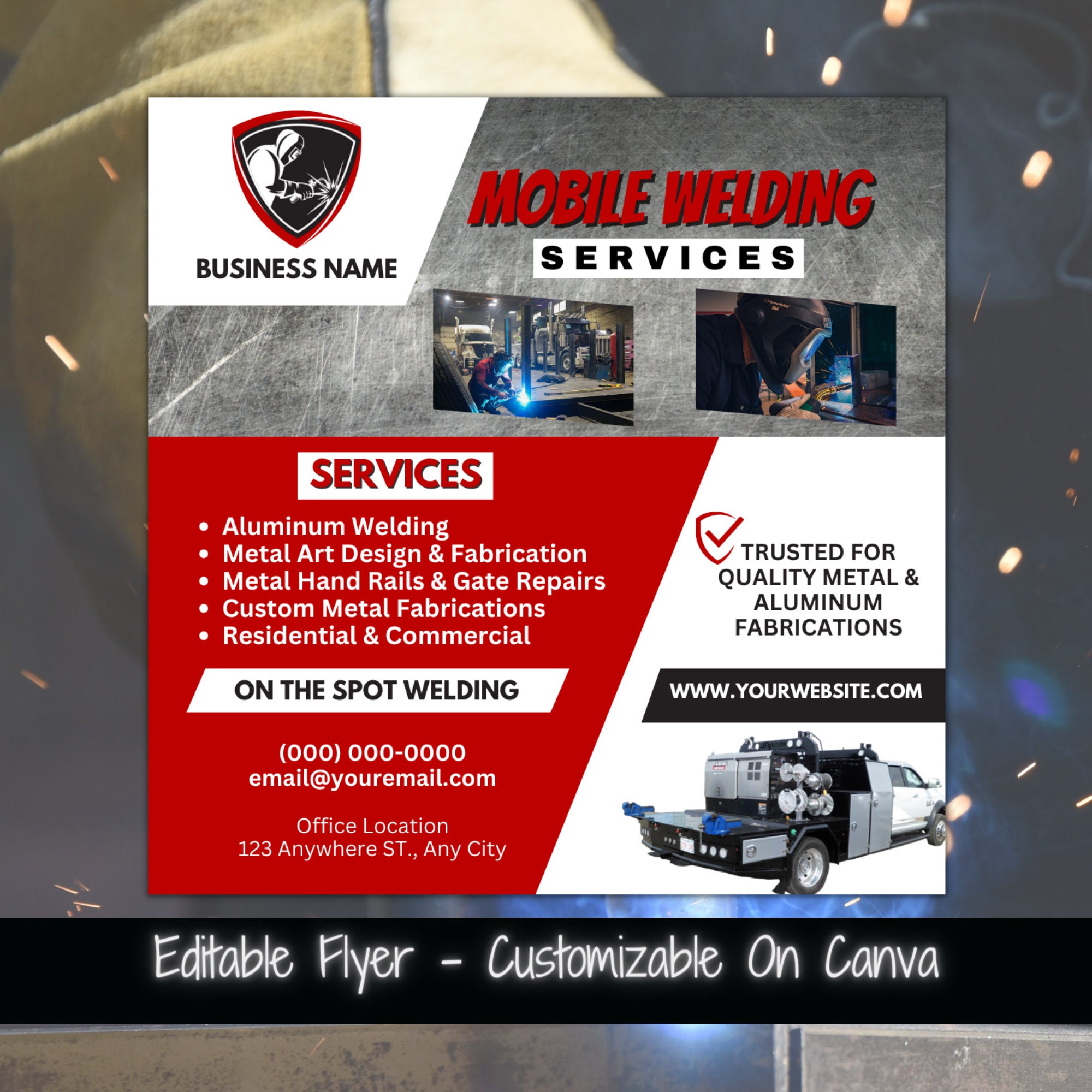
Report this page